NPK Production Line
WHAT IS THE BENEFIT OF MAKING NPK FERTILIZER?
Plants cannot get enough NPK elements from the soil. By producing NPK fertilizer, the soil can get enough nutrients. Because fertilizer can help to boost crop production and to keep people fed. Plants need 17 kinds of nutritional elements to grow, while they can obtain 14 kinds from the soil and the other three need to get from water and air. In our previous post, you can learn about how we help one Australian customer set up an 5tph NPK fertilizer production line.
As a growing population, it is going to exceed 9 billion by 2050. By then, fertilizer will be more needed than ever before.
Studies show that the NPK ratio is ideal when it’s 3-1-2 in most cases.
Nevertheless, the actual ratio sometimes varies with different kinds of plants. For example, the NPK ratio for corn and lawns has higher percentages of nitrogen.
The best NPK ratio for your plants
You need to take a soil test to determine the best NPK ratio for your plants. This will help you know what nutrients are needed. If there’s large amounts of phosphorous in your soil, then you need find a NPK fertilizer with a higher ratio of nitrogen.
HOW DO YOU MAKE NPK FERTILIZER?
To make NPK fertilizer, you’d better learn about the NPK production line first. First, you need to know the raw materials for making NPK fertilizer and then know the main equipment in the NPK production line. With all the information, you need to decide what end products you want. In the next chapters, we will introduce the process of producing NPK powder and granulated NPK fertilizer.
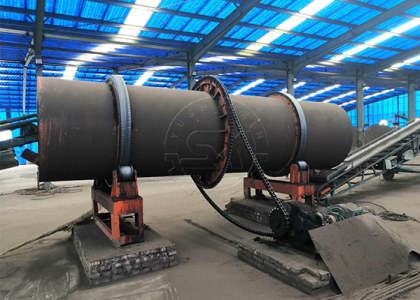
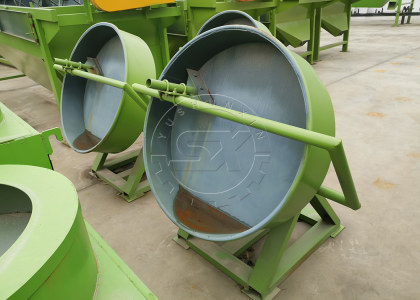
WHAT ARE THE RAW MATERIALS FOR MAKING NPK FERTILIZER?
You can make NPK fertilizer from many raw materials. Following are the raw materials of nitrogen, phosphorous, and potassium.
N: Urea, Di Ammonium Phosphate, Ammonium Chloride, Ammonium Nitrate, Ammonium Sulphate, Mono Ammonium Phosphate Etc.
Phosphorous as P2O5: Single Super Phosphate, Triple Super Phosphate, etc.
Potash as K2O: Potassium Chloride, Potassium Sulphate, etc.
WHAT ARE MAIN EQUIPMENT FOR NPK PRODUCTION LINE?
The main equipment in the NPK production line is a belt conveyor, mixer, rotary drum granulator, hot stove, rotary dryer, rotary cooler, dust collector, screener machine, crusher rotary coating machine, and packing machine.
HOW TO PRODUCE NPK POWDER?
The powder NPK production line is simple. You need to know what materials you will use and in what amounts. Then you need to crush raw materials into a fine powder and then blend all the materials. As for crushers, MFP recommends three types of crushers that are commonly used in NPK compound fertilizer production.
3 TYPES OF CRUSHERS
The first type is the urea crusher. When choosing urea as a raw material of nitrogen, this type is the best choice. The speed and diameter of the urea crush are adjustable. It crushes materials by the gap between the roller and the concave. The inlet size should be smaller than 4mm and inlet moisture should be less than 5%. The output size of this machine is 0.3-0.5mm.
The second type is the cage crusher. It is widely used in compound fertilizer crushing and also as a medium-sized horizontal cage bar crusher. Among the three crushers, the cage crusher allows the largest inlet sizes (about 280*320mm). Furthermore, it has a compact structure(1500*1500*1500mm).
The third type is a chain crusher. We can divide it into two types: vertical chain crushers with a single rotor and horizontal chain crushers which with double rotors. You can use it in compound fertilizer production and the crushing of return materials after the screening.
After crushing raw materials, you need to batch them and then mix them. As for the mixing process, double shafts horizontal mixer, BB fertilizer mixer, and drum type BB fertilizer mixer are suitable for mixing NPK fertilizer. BB fertilizer overcomes the mixtures chromatography and distributaries phenomena caused by different proportions of raw materials. Otherwise, you can use drum type BB fertilizer mixer in large-scale NPK production, for it can achieve continuous production and the output can reach 30-40 tons per hour.
HOW TO MAKE GRANULATED NPK FERTILIZER?
A granulator can help you make NPK fertilizer pellets from powder. There are mainly two ways to make pellets: wet granulation and dry granulation. In the dry granulation process, you can choose our double roller granulator machine. It has a compact structure and high-efficiency characteristics. Without the drying process, it is convenient and fast. The rollers are stainless and can prevent wear and tear for a long time. The end product size of this double roller granulator machine is 3-10mm.
If you make pellets by wet granulation, we recommend you choose a rotary drum granulator. Its capacity can reach 30 tons per hour. After wet granulating, you need to dry the particles under the moisture of 20% so as to pack and store them. You can use a rotary drum drying and cooling machine to reduce moisture.
That’s all about MFP’s NPK production line. We provide both large-scale and small-scale production lines. If you have other questions about making NPK fertilizers, please don’t hesitate to contact us.