Bulk Blending Fertilizer Production Line
This Bulk blending fertilizer production line can assemble various ratios of compound fertilizer and it can also meet different scales of production. On this page, you will know how to produce bulk blending fertilizer with fertilizer equipment. As a fertilizer equipment manufacturing specialist, MFP factory will present you with a fundamental and detailed making process.
Advantages Of Making Bulk Blending Fertilizers
Bulk blending fertilizers provide farmers with a correct proportion of nitrogen, phosphorus, potassium, and micronutrients. Thus, producing bulk blending fertilizer can greatly promote crop yields. With the increasing use of soil analysis, bulk blending fertilizer is often the best solution to give what their crops need.
What’s more, it can fulfill almost any soil analysis requirement.
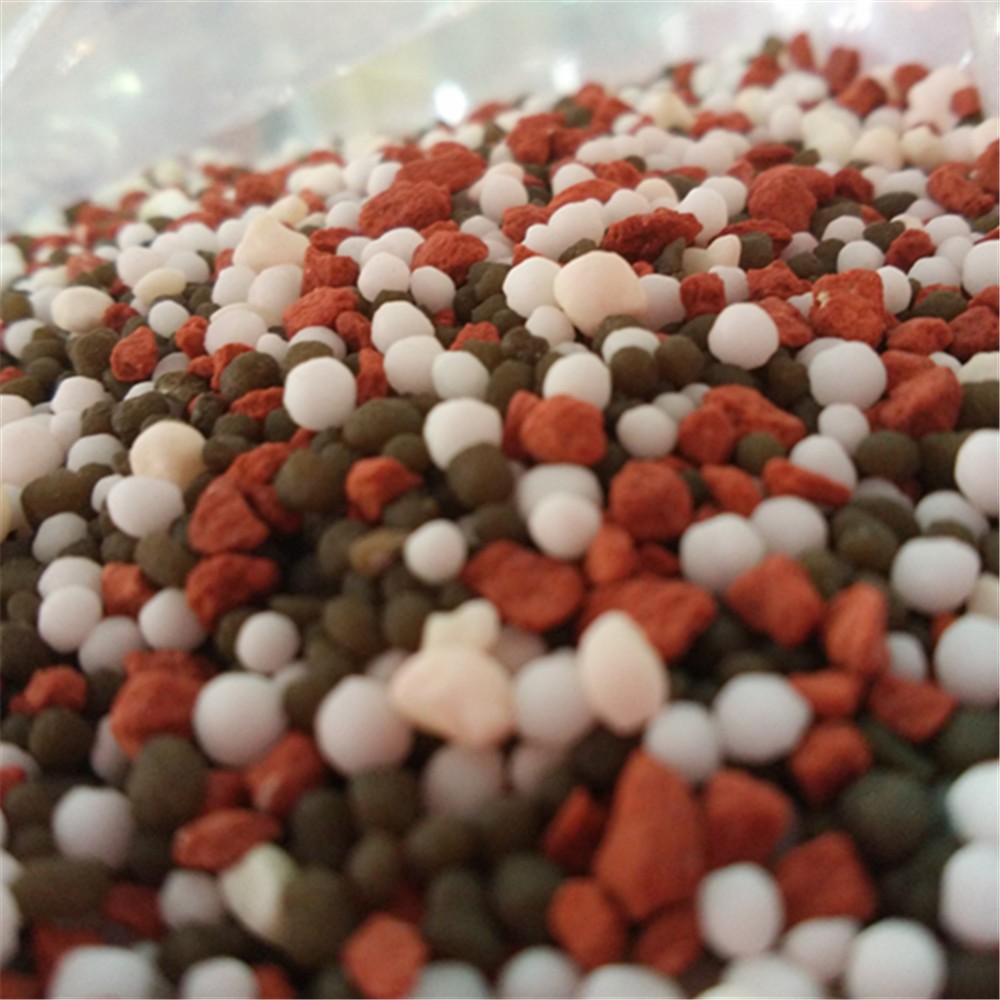
Granulation Process In Bulk Blending Fertilizer Production Line
Granulation: The uniformly mixed and crushed material is sent to the granulator through the belt conveyor for granulation. In wet granulation, drum type granulator and disc granulators are favored. The former can suit large-scale production, while the latter can suit many scales production and is easy to operate. This step is essential in the BB fertilizer granulation production process.
Granule drying: Dry the moisture contained in the granules to increase the strength of the granules and facilitate storage. Generally, a drum dryer is popular because it has advantages such as low energy consumption and high capacity.
Granule cooling: After drying, the temperature of the fertilizer pellets is high and easy to agglomerate. Therefore, you need to cool them to keep them from sticking.
Finished particle coating: BB fertilizer manufacturers generally use a coating machine to increase the brightness and roundness of the particles. Finally, the whole granulation process comes to an end and you are able to pack the final products.
Quantitative packaging of finished granules: The finished granules are sent to the silo for temporary storage through a belt conveyor. Then they are connected to electronic quantitative packaging scales and sewing machines for automatic quantitative packaging and sealing.
Wet And Dry Granulation Of Bulk Blending Fertilizer
According to the granulation method, there are wet granulation and dry granulation in bulk blending fertilizer production line. They need different fertilizer equipment. In the next paragraph, we will show you how these two granulation methods work.
Bulk Blending Fertilizer Wet Granulation Production Line
The process of bulk blending fertilizer wet granulation production line goes like this: raw material batching, full blending, crushing, granulation, drying, cooling, coating, and packaging. Let’s take a look at the eight procedures and what kind of equipment they need.
Bulk Blending Fertilizer Dry Granulation Production Line
In BB fertilizer dry granulation process, double roller extrusion granulator is often used, so it is also called extrusion granulation production line. The fertilizer equipment of the dry granulation process has low investment, quick effect, and good economic benefit. The whole set of equipment has a compact layout and advanced technology. It can save your energy saving and consumption.
In BB fertilizer dry granulation process, double roller granulator is the most common. MFP also produces high-quality double roller granulators. The raw materials of double rollers are stainless steel. So it can last for a long time. Moreover, you can change the rollers if there’s wear and tear. This granulator can make pellets of 3-10 mm.
The ball socket on the roller is adjustable, you can customize any kinds of pellet you want, such as pillow shape, semicircle shape, and stick shape.
The dry granulation production line doesn’t need a dryer or cooler, so the whole production is more efficient than the wet granulation production line. Then, what are pros and cons of dry granulation?
Pros And Cons Of BB Fertilizer Dry Granulation:
Extrusion granulation does not need to heat and humidify the material and is also suitable for granulation containing heat-sensitive materials, such as ammonium bicarbonate and some organic fertilizers.
There is no waste water or exhaust gas discharged during the production process, which will not pollute the environment.
The shape of extrusion granulation products is not as round as that produced by traditional methods such as drum granulation. If there is a chemical reaction between the ingredients, the granules may collapse.
5 Things Need To Pay Attention When producing bB fertilizer
- First of all, choose the raw materials reasonably, that is, choose the raw materials that are not easy to agglomerate. For example, the fertilizer with humic acid, and the fertilizer with amino acid are not easy to agglomerate. In addition, the material you select should be as dry as possible.
- Second, you should choose the right production time. You should avoid rainy and hot seasons to produce your BB fertilizer because high temperatures and moisture are conducive to agglomeration. Therefore, avoiding these situations will lower the probability of agglomeration. because the air humidity is low and the temperature is not high, which is not conducive to agglomeration.
- Third, you can add some anti-caking elements, such as talcum powder, humic acid, and other powders that are not easy to agglomerate, and they will act as a bridge breaker in the middle. Also, choosing a high-quality crusher is also important. The cage crusher of MFP company with two sets of cages can greatly reduce the caking problems. You can also add some surfactants to prevent caking.
- Fourth, the granulation technology of BB fertilizer can prevent agglomeration. Because the contact area between round grains is small, it is not easy to crystallize and agglomerate. Therefore, disc granulation is the best way to prevent caking.
- Finally, you should pack the compound fertilizer reasonably to prevent extrusion. The packaging materials should mainly prevent moisture absorption and ventilation, and prevent excessive extrusion during transportation and storage, which can also effectively prevent agglomeration. To achieve this, you’d better use a rotary drying machine. Otherwise, if your bulk blending fertilizer production line has a large capacity, you also need a rotary cooling machine to further reduce the water moisture.